IMPRÉGNATION VPI
À PROPOS DU PROCÉDÉ VPI
Wajax | Delom possède quatre cuves d'imprégnation sous vide et pression (VPI) dans ses divers ateliers, la plus imposante ayant 4,9 m de diamètre et une profondeur de 3,7 m (16 pieds x 12 pieds). Dans l'optique de « Réparer pour ne plus réparer », les usines de Wajax | Delom utilisent des vernis à base d'époxy ayant une haute viscosité, permettant de satisfaire aux plus hauts critères de qualité d'un bobinage.
VPI signifie Vacuum Pressure Impregnation (système d’imprégnation sous vide et pression). Il s’agit d’un procédé par lequel un rotor ou un stator entièrement bobiné de conception VPI est submergé dans une résine. Par l'entremise d'une combinaison de cycles de séchage, d'imprégnation sous vide ABSOLUE, de fortes pressions et de polymérisations, les vernis s'insèrent dans toutes les cavités du bobinage, garantissant une performance supérieure.
Un système d’isolation VPI à base d'époxy réponds aux quatre besoins essentiels d'un bobinage durable et efficace. Il offre un bouclier optimal au bobinage dans les environnements abrasifs et poussiéreux tout en améliorant également la rigidité mécanique de l’ensemble de l’équipement rotatif.
UN SERVICE ENTIÈREMENT INTÉGRÉ
Wajax | Delom est votre expert et votre guichet unique pour les unités critiques et les moteurs électriques de toutes tensions. Avec l’une des cuves VPI les plus imposantes en Amérique du Nord, nous pouvons relever n’importe quel défi et offrir une expertise à valeur ajoutée à tout projet de bobinage.
Notre connaissance approfondie des usines de nos clients, notre compréhension approfondie du fonctionnement de tous les moteurs électriques, les analyses de causes de bris ainsi que notre expertise sur les procédés d’isolation nous permettent d’effectuer la recette de bobinage la plus adéquate et avant-gardiste.
- Grande capacité de bobinage
- Moteurs électriques et générateurs jusqu’à 13,8 kV
- Recette adaptée à chaque condition d'opération
- Rétro-ingénierie des bobinages
- Modernisation du système d’isolation
Nos travaux de réparation et de bobinage sont toujours élaborés sur mesure, selon les conditions d’opération réelles.
AVANTAGES D’UN SYSTÈME D’ISOLATION VPI
- Protection optimale contre les effets corona
- Excellente rigidité diélectrique à la masse et entre spires
- Excellente dissipation thermique des bobinages
- Meilleure stabilité mécanique
- Meilleure performance en milieu corrosif, abrasif ou poussiéreux
- Augmentation des MTBR pour l'entretien des bobinages dans les environnements contaminés
- Augmentation de la durée de vie du bobinage
- Procédé garantissant l'étanchéité contre l’humidité et les produits chimiques
- Réduction du coût total de propriété de l’unité (TCO)
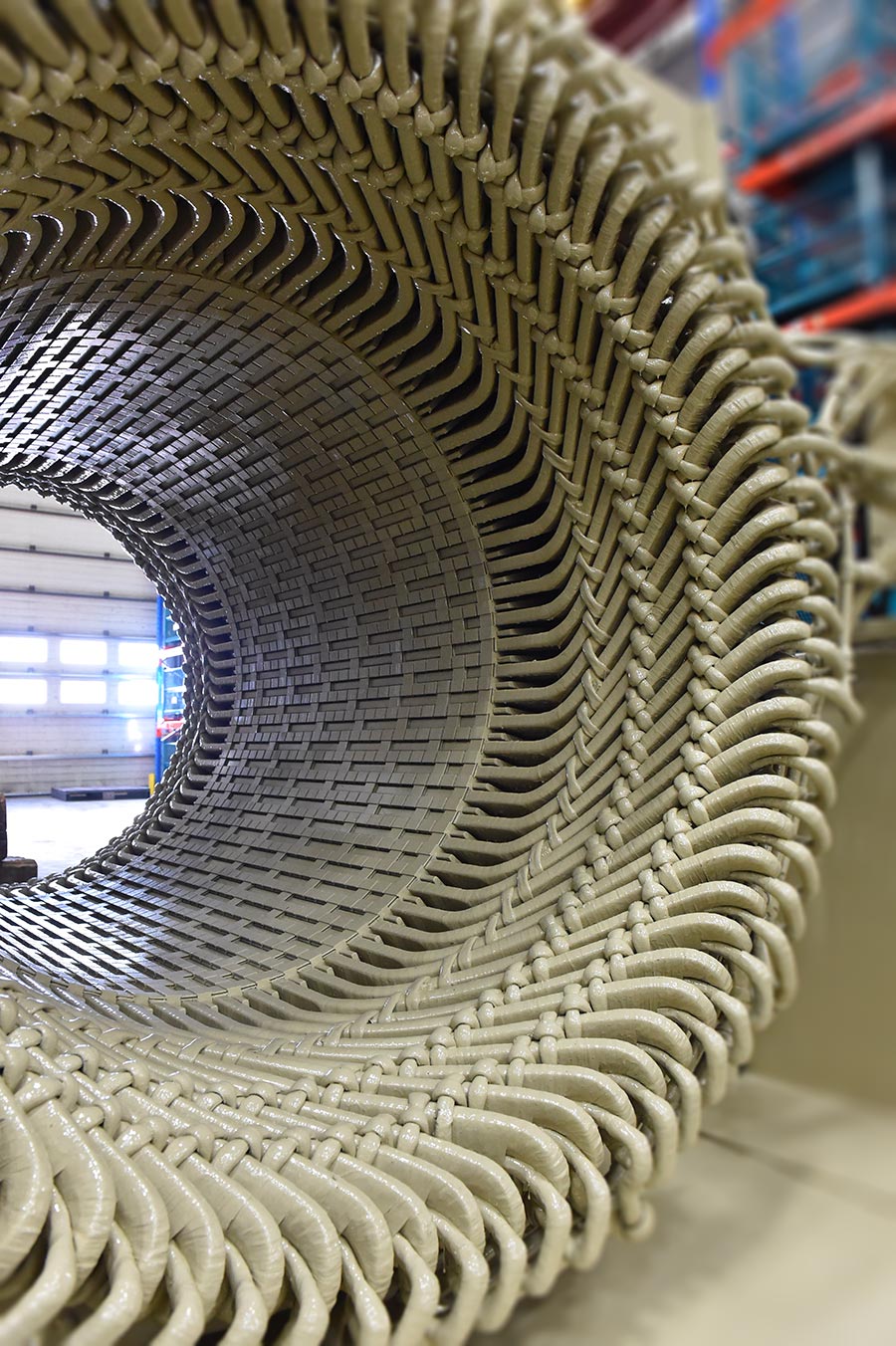
ATELIERS SPÉCIALISÉS