REVERSE ENGINEERING AND MANUFACTURING OF CUSTOM PARTS
Wajax | Delom offers a full range of services for the reverse engineering and manufacturing of custom components. Our seasoned experts make full use of their vast experience in electromechanics, mechanical manufacturing, winding, welding, engineering and design by proposing innovative solutions all over the world.
Over the years, we have developed solutions adapted to all types of climates and environments, from West Africa to South America... all the way up to the Arctic.
Many industrial sites, including mines, steel mills, pulp and paper mills, petrochemical plants, hydroelectric power plants and wind farms, were built several decades ago. The maintenance teams at these sites face the daily challenge of keeping the original electric motors, generators and other rotating equipment available for production and avoid unplanned downtimes.
- Reverse engineering and manufacturing of complete electric motors
- Reverse engineering and manufacturing of custom stators
- Reverse engineering and manufacturing of custom rotors
- Reverse engineering and manufacturing of bases and pedestals
- Reverse engineering and manufacturing of custom exciters
- Reverse engineering and manufacturing of ventilation units
- Reverse engineering and manufacturing of impellers and agitators
- Reverse engineering and replacement of wye ring (wind power)
- Reverse engineering of all types of windings
- Frequency and/or speed change
- Power change
- Voltage change
- Power supply change (use with VFD)
- Conversion of DC excitation systems into rotating diodes (brushless)
- Manufacture and assembly of large-scale welded parts
- Analysis and optimization of insulation processes for all types of windings
- Quick on-site measurement with CMM (Leica laser tracker, FARO arm)
- 3D design by our experts
- Magnetic simulation
- Internal project management team
- Complete final testing
- Unique projects or projects or low repeatability
- Internationally recognized certifications
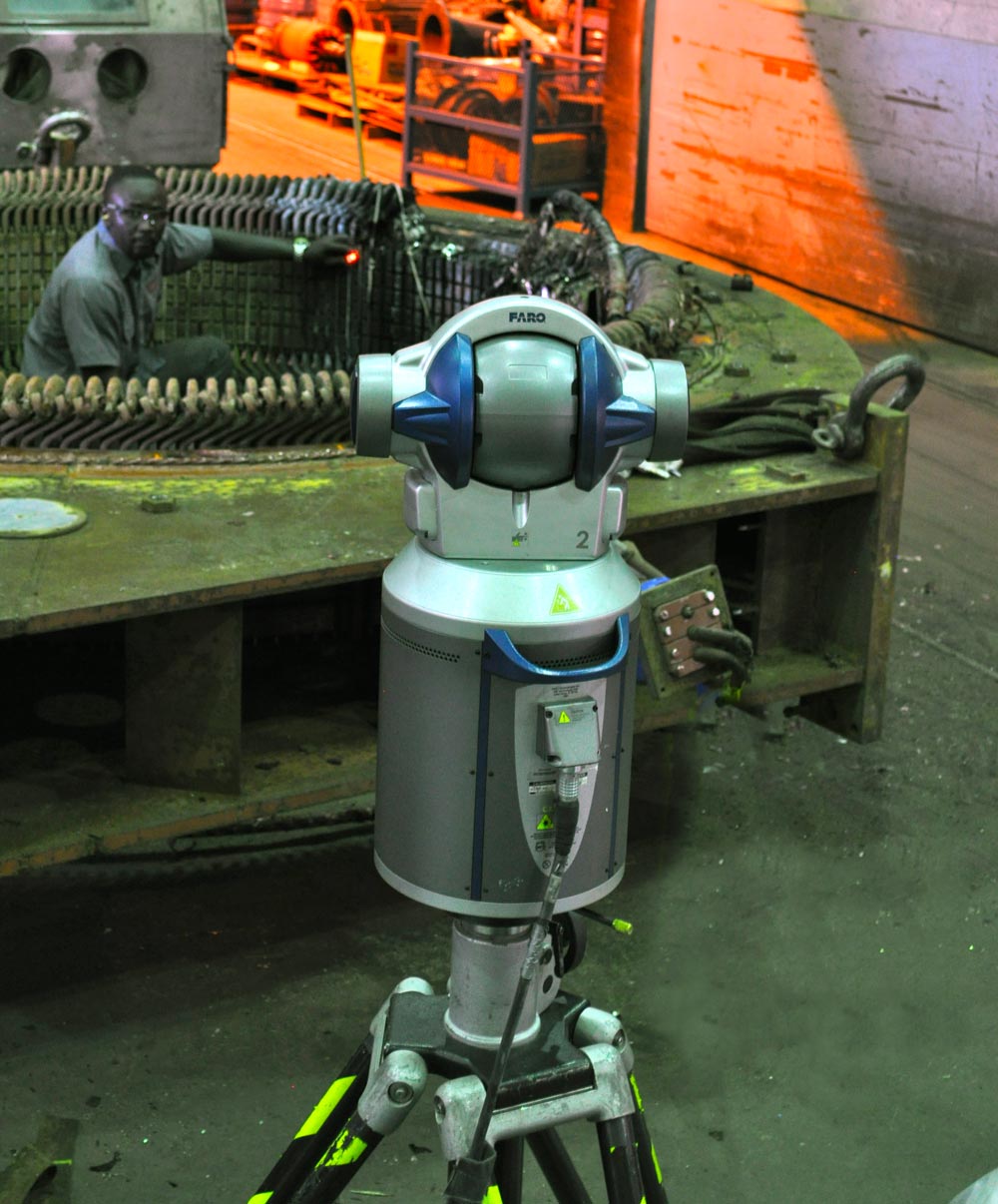
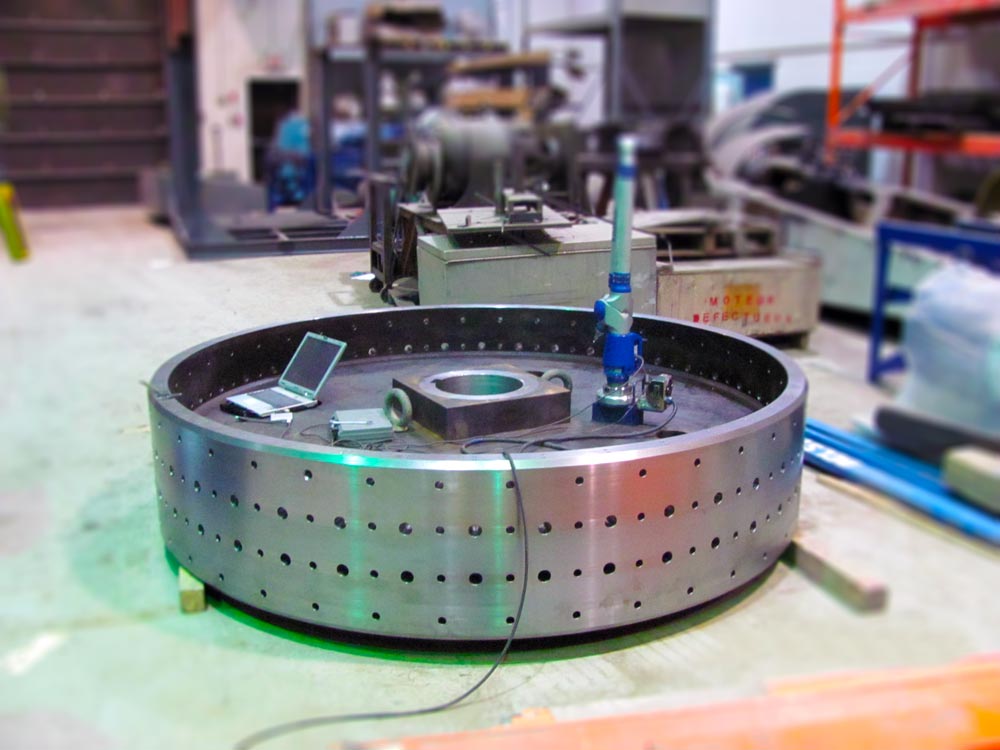
UP-TOWER WIND GENERATOR RETROFIT
- Wye ring retrofit for Hitachi wind power generator
- Wye ring retrofit for GE wind power generator
- Wye ring retrofit for ABB wind power generator
- Rotor cables retrofit for ABB, GE and Hitachi wind power generators
- Brush/brush holder retrofit and full analysis
CONVERTING A DIRECT CURRENT EXCITER TO A ROTATING DIODE
The conversion of a DC exciter to a rotating diode offers many advantages other than the obvious saving of maintenance time due to the removal of the commutating system, which results in increased availability of the machine.
In fact, this patented process, developed in partnership with Hydro-Québec and the University of Artois, will use the same structure again and will have pretty much the same weight, eliminating the need for structural evaluation, which can be long and expensive. The exciter stator and rotor windings are completely redesigned to work with a diode bridge instead of carbon brushes and a commutator. The main shunt breaker is also removed.
Each exciter presenting its own difficulties, the entire design is provided by the experienced team of Wajax | Delom and entirely made in house.
A conversion to a rotating diode exciter should always be considered when refurbishing a small or medium-sized hydropower plant, as it offers many advantages:
- Increased machine availability
- Elimination of conductive carbon dust contamination in the exciter and alternator
- Maintenance shutdowns are significantly reduced
- Use of the original structure
- Same weight constraint on the main shaft
- Same response time on the transport network
- Elimination of the main circuit-breaker
work – Project
- Removal of shunt breaker
- Measurements at the plant
- Electrical and mechanical design
- Electrical and mechanical simulation
work – Stator
- Removal of interpoles
- Manufacturing of new VPI poles
- Machining of the housing
Work – Rotor
- Removal of the commutator
- Removal of collector rings
- Manufacturing of new coils and complete rewinding
- VPI insulation
- Installation of the diode bridge
SPECIALIZED WORKSHOPS